The Manufacturing Process of Polypropylene Yarn
- Sparetex
- Mar 1
- 2 min read
From Raw Materials to Finished Yarn: A Step-by-Step Guide to How Spare Tex Manufactures Polypropylene Yarn
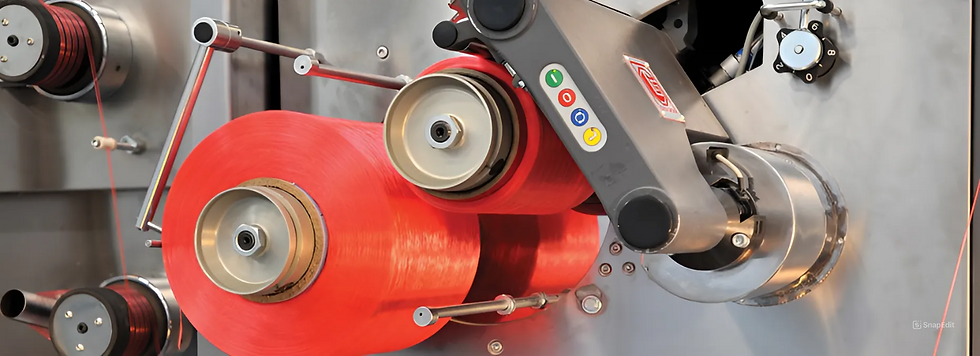
At Spare Tex, we take pride in our meticulous manufacturing process that transforms raw materials into high-quality polypropylene yarn. Every step is carefully designed to ensure durability, consistency, and performance. Today, we’re taking you behind the scenes to show you how polypropylene yarn is made – from raw materials to the final product.
Step 1: Sourcing High-Quality Raw Materials
Our process begins with polypropylene pellets, derived from propylene gas through polymerization. These pellets are the foundation of our yarn, and we ensure they meet the highest quality standards before they enter our production line. At Spare Tex, we believe that quality starts with the right raw materials.
Step 2: Melting and Extrusion
The polypropylene pellets are fed into our state-of-the-art machinery, where they are melted at high temperatures. The molten polymer is then extruded through spinnerets – specialized nozzles that shape the material into fine, continuous filaments. This step ensures uniformity in thickness and strength, setting the stage for high-quality yarn.
Step 3: Drawing and Stretching
The filaments are drawn and stretched to align the polymer chains, enhancing the yarn’s tensile strength and durability. This step is crucial for creating yarn that can withstand heavy use without compromising on performance.
Step 4: Texturizing (Optional)
For applications that require softness and elasticity, such as apparel or home textiles, the yarn undergoes texturizing. This process adds bulk and texture, making the yarn more versatile and comfortable.
Step 5: Cooling and Solidification
The yarn is cooled to solidify its structure, ensuring it retains its shape and strength. This step is critical for maintaining the yarn’s integrity during further processing and end-use applications.
Step 6: Winding and Packaging
Finally, the yarn is wound onto spools or bobbins using automated winding systems. Each spool is inspected for quality, ensuring that it meets Spare Tex’s rigorous standards before being packaged for delivery.
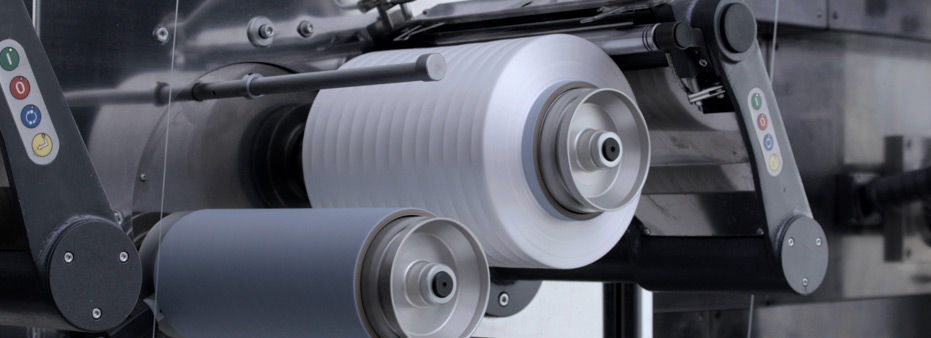
Why Our Manufacturing Process Matters
At Spare Tex, we don’t just produce yarn – we craft solutions. Our advanced manufacturing process ensures that every strand of polypropylene yarn is strong, durable, and ready to meet the demands of your industry.
The Final Product
The result is a high-performance yarn that’s lightweight, moisture-resistant, and incredibly versatile. Whether it’s used in carpets, textiles, or industrial applications, Spare Tex’s polypropylene yarn is built to last.
Our Commitment to Quality
From raw materials to finished product, we prioritize quality at every step. Our team of experts uses cutting-edge technology and rigorous testing to ensure that our yarn meets the highest standards.
What’s Next?
Now that you know how Spare Tex manufactures polypropylene yarn, stay tuned for Day 4, where we’ll explore the advantages of polypropylene yarn over other synthetic fibers. You’ll discover why it’s the preferred choice for industries worldwide.
Final Thoughts
The manufacturing process of polypropylene yarn is a blend of science, technology, and craftsmanship. At Spare Tex, we’re proud to deliver a product that’s not only high-quality but also sustainable and cost-effective.
When you choose Spare Tex’s polypropylene yarn, you’re choosing innovation, reliability, and excellence.
nice